Table Of Content

Destructive testing involves physically testing the weld to assess its mechanical properties and performance. This testing is typically performed on test specimens or samples that are representative of the weld joint. Common destructive testing methods include tensile testing, bend testing, impact testing, and hardness testing.
Architectural Metalwork
New Zeta Fresh Air Helmets and Beta Art helmet designs - Cision News
New Zeta Fresh Air Helmets and Beta Art helmet designs.
Posted: Tue, 13 Feb 2024 08:00:00 GMT [source]
If the weld metal's strength exceeds the base metal strength, then increasing the weld's size further will not increase the strength of the connection. The weld size for which the weld base metal strength equals the base metal strength is known and the LARGEST EFFECTIVE size. Rounding up to the nearest 16th of an inch results in the largest effective weld size.
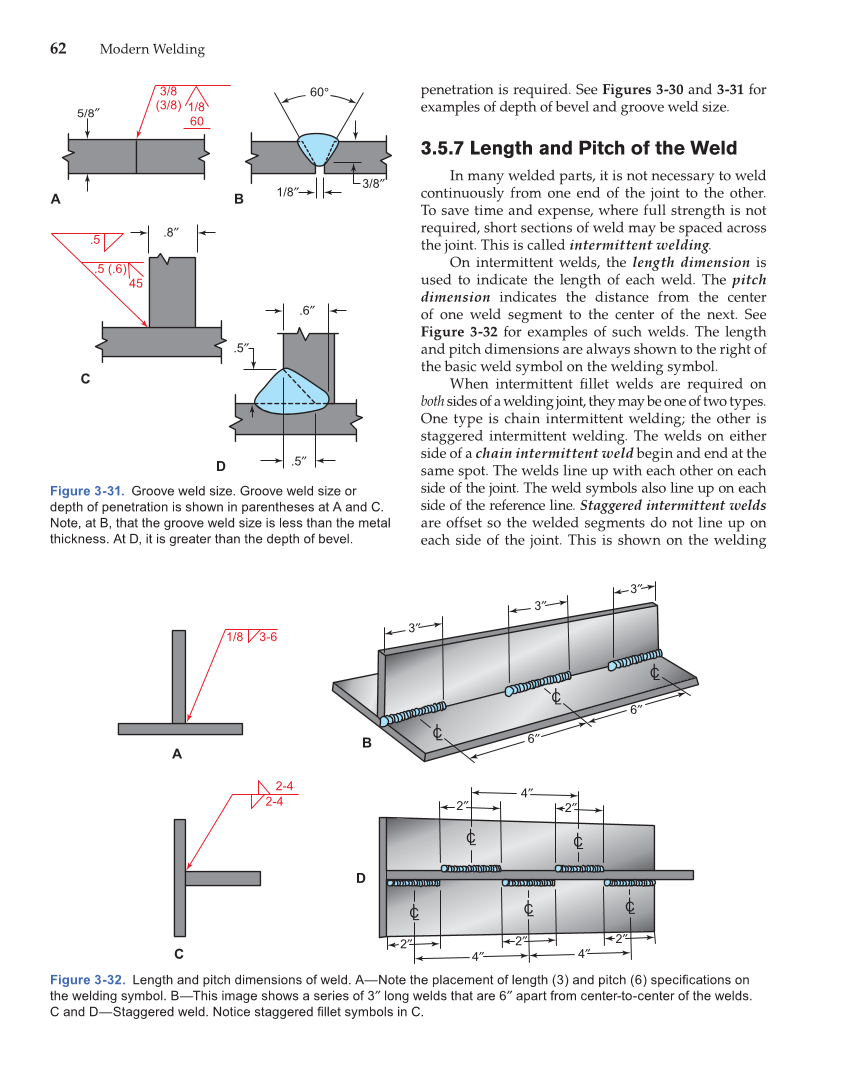
Metallurgy
CRC Evans takes unique approach to hydrogen service weld design - The Australian Pipeliner
CRC Evans takes unique approach to hydrogen service weld design.
Posted: Wed, 15 Nov 2023 08:00:00 GMT [source]
By considering factors such as weld size, shape, and reinforcement, designers can enhance the weld’s ability to withstand cyclic stresses over a prolonged period. Lastly, addressing distortion, which refers to the deformation or misalignment of welded parts during the welding process, is essential. Minimizing distortion requires a thoughtful design that considers pre-welding preparation, selection of welding methods, and control measures to counteract the thermal effects induced by welding. The principles of welding design encompass vital aspects such as strength, fatigue resistance, and distortion control.
Travel Speed
Common shielding gases include argon, helium, and carbon dioxide, each offering specific advantages and limitations. Proper selection and regulation of the shielding gas are essential for achieving a clean, defect-free weld with optimal mechanical properties. By classifying welding techniques into distinct categories like fusion welding, pressure welding, and brazing/soldering, it becomes easier to identify the appropriate method for specific applications.
Discover the Stunning World of Designer Charm Bracelets
It is influenced by factors such as welding current, voltage, travel speed, and electrode size. Controlling heat input is essential for achieving proper fusion and avoiding issues such as excessive distortion, cracking, or lack of penetration. The specific heat input requirements vary depending on the material being welded and the desired weld properties. Choosing the appropriate welding technique is crucial for achieving desired results in weld design. Different welding techniques offer various advantages and limitations, and selecting the right technique depends on factors such as material properties, joint configuration, and project requirements. Different welding processes have varying heat inputs, which can influence the metallurgical properties of the weld.
Adherence To Regulations And Deadlines For Weld Design Projects
Achieving a strong and durable weld starts with proper joint preparation. This section will guide you through the essential steps involved in preparing the weld joint, including cleaning, edge preparation, and fit-up. By following best practices in joint preparation, you can enhance the quality and integrity of your welds.
There are certain slot shapes which can promise more accuracy, but at the cost of strength. We feature in our store some of our best software to design, collaborate and innovate throughout the entire product lifecycle.
Designing for Manufacturability
The truth is there are many tricks that you can use to minimize or even eliminate weld distortion. Every engineer learns the basics of welding in college, but little else. When faced with real world weldment problems, we quickly turn straight to FEA.
GTAW offers several advantages, including excellent control over heat input, minimal distortion, and the ability to weld a wide range of materials, including exotic alloys. It is particularly suitable for applications that require superior weld quality and aesthetics, such as aerospace and nuclear industries. However, GTAW has a slower deposition rate compared to GMAW, making it less productive for certain applications. This also raises the point that the fillet weld is extremely difficult to volumetrically examine using non-destructive testing techniques to confirm its internal soundness. This applies particularly to the root region where it is not possible to measure, with any degree of precision, any lack of fusion, slag entrapment etc.
We will cover numerous mechanical and thermal methods for dealing with distortion. The welding process introduces complications because of the high temperatures needed. It takes too long to perform and there are too many variables to consider.
Welds in aerospace applications must withstand extreme operating conditions, including high temperatures, pressure differentials, and vibrations. Advanced welding techniques, such as electron beam welding or friction stir welding, are often employed to achieve strong and defect-free welds in materials like aluminum, titanium, and superalloys. When it comes to weld design, it is crucial to have a solid understanding of the fundamental concepts. The most common types include butt joints, lap joints, corner joints, and T-joints.
No comments:
Post a Comment